Metal Stamping Overview
What Is Metal Stamping?
Metal stamping is a manufacturing process that utilizes dies and high-pressure machinery to cut, emboss, or shape metal sheets into specific forms and designs. This method is fundamental in creating durable, high-precision parts across various industries, including automotive, aerospace, electronics, and medical devices. By applying significant force, metal stamping transforms flat metal sheets into complex shapes with remarkable accuracy and repeatability. This process not only supports large-scale production but also allows for intricate detailing and consistency in parts, making it a critical component of modern manufacturing techniques.
Worthy Hardware produces kinds of stamping parts with steel, stainless steel, brass, copper and aluminum in short run and long run orders. Our machines ranges from 25 tons to 500 tons, and the max thickness could reach to 0.5inch.
Metal Stamping Process
Metal stamping operates through a series of well-defined steps, utilizing specialized machinery and tools to transform flat metal sheets into precise shapes and designs. Initially, a metal sheet is positioned in a stamping press where dies and tools are ready to enact their function. When the press is activated, it exerts substantial force, causing the die to cut, bend, punch, or emboss the metal into the predetermined shape. This process can be completed in a single stage or through multiple stages, depending on the complexity of the part being produced.
Each die set is meticulously engineered to ensure the metal forms accurately to the specified dimensions and tolerances. The capability to perform operations such as blanking, piercing, forming, and drawing in rapid succession makes metal stamping highly efficient for mass production. Furthermore, advancements in technology have enhanced precision, allowing for the creation of components with intricate features and tight tolerances. Post-stamping processes may include deburring, cleaning, and finishing, which further refine the quality and functionality of the stamped parts.
Metal Stamping History
Metal stamping traces its origins back to the industrial revolution, evolving from basic manual hammering to sophisticated presses. This transformation has enabled the mass production of metal parts, revolutionizing manufacturing sectors by providing faster, more precise, and cost-effective solutions for creating complex components.
Advantages Of Metal Stamping
Ideal for high-volume production, metal stamping significantly lowers the cost per unit through economies of scale;
Achieves parts with tight tolerances and uniform quality;
Offers fast production rates, ensuring quick turnaround times and improving manufacturing efficiency.
Disadvantages Of Metal Stamping
High tooling and die caost, it it less cost-effective for small production runs.
Extremely intricate designs may require additional processing or specialized tooling, increasing production time and costs.
Need workers to make the regular maintenance of stamping presses and dies.
Types Of Metal Stamping
Metal stamping encompasses a range of processes, each tailored to meet specific manufacturing needs and design requirements. The primary types include:
Progressive Stamping
Progressive stamping utilizes a series of stations within a single press, each designed to perform a specific operation—cutting, bending, punching, or coining—on a metal strip as it passes through. This sequential approach ensures continuous production and intricate part detailing, making it ideal for complex component fabrication.
This method excels in minimizing material wastage and maximizing productivity. By integrating multiple tasks into one continuous operation, progressive stamping reduces production times and costs. Its capability to maintain tight tolerances and consistent quality across large batches underscores its value in industries demanding precision, such as automotive and electronics.
Deep Draw Stamping
Deep draw stamping is a specialized metal forming process that is utilized to create deep, hollow parts exceeding their diameter. This technique involves pulling a sheet metal blank into a die through a punch, forming a cup-shaped part without altering the material thickness.
Deep draw stamping is distinguished by its ability to produce components with high depth-to-diameter ratios, making it ideal for manufacturing parts like automotive bodies, kitchen sinks, and various metal enclosures used in electronics and appliances.
Fourslide Stamping
Fourslide stamping, also known as multislide or four-way stamping, is a versatile and efficient metal forming process uniquely designed to handle complex parts with multiple bends and angles. This technique employs a series of horizontal slides — four in total — that move in and out of the working area, allowing for precise manipulation of the metal workpiece from multiple directions.
This method is particularly beneficial for producing small, complex parts in high volumes, such as brackets, clips, and connectors, across various industries including electronics, automotive, and medical devices.
Transfer Die Stamping
Unlike progressive stamping, which processes the metal strip through various stations within a single die, transfer die stamping uses individual dies for each operation. Here, parts are transferred from one station to the next by mechanical handlers, enabling each piece to undergo multiple operations such as punching, bending, and trimming within separate but sequentially arranged dies.
Short Run Stamping
Short Run Stamping caters to low-volume production needs, offering flexibility and reduced tooling costs. Ideal for custom or prototype parts, this process allows for rapid adjustments and minimal investment. It suits projects requiring fast turnaround times and those in the developmental stages, providing precision and quality without the necessity for large-scale production setups.
Long Run Stamping
Long Run Stamping is optimized for high-volume production, significantly reducing the per-unit cost through economies of scale. This process is ideal for parts with consistent demand, utilizing dedicated tooling to ensure high precision and efficiency. It supports continuous operations, making it a staple in industries needing vast quantities of identical components with stringent quality standards.
Metal Stamping Techniques
Blanking
Blanking is a metal stamping technique where a flat piece is cut out from a larger sheet of metal through a die. It’s the first step in creating parts with precise dimensions and smooth edges, ideal for further processing. This method is widely used for high-volume production of consistent shapes.
Punching
Punching is a fundamental metal stamping technique that involves creating holes or cutouts in a piece of metal by forcibly driving a punch through it and into a die beneath. This process is highly efficient for adding functional features to metal parts, such as ventilation holes or slots, and is versatile enough to be applied to various materials and thicknesses.
Coining
Coining is a precise metal stamping technique that utilizes immense pressure to plastically deform a metal piece, imprinting detailed designs or shapes without removing material. It is ideal for creating parts with fine features, such as embossed letters, logos, or intricate patterns.
Bending
Bending is a versatile metal stamping technique that shapes metal sheets or strips by applying force to create a desired angle or curve. This process is fundamental for fabricating components with specific geometrical profiles, such as brackets or enclosures.
Flanging
Flanging is a metal stamping process that involves bending the edge of a metal part to form a flange or rim. This technique is crucial for adding strength, rigidity, or attachment points to components, and for facilitating seamless assembly.
Hydroforming
Hydroforming is an innovative metal forming technique that uses high-pressure hydraulic fluid to shape metals into complex, lightweight, and structurally strong components.It is Ideal for producing seamless and intricate shapes.
Embossing
Embossing creates raised or recessed designs on a metal surface, adding texture or decorative patterns. This technique enhances both the aesthetic appeal and functional attributes of metal parts, such as improving grip.
Curling
Curling is a metal forming technique that rounds the edges of a metal part into a tubular profile, enhancing strength and eliminating sharp edges. This process is crucial for safety and aesthetic purposes in various applications, including handles, knobs, and trim components.
Piercing
Piercing in metal stamping involves creating holes or shapes in a metal workpiece using a punch and die. Unlike drilling, piercing can produce complex shapes efficiently and is ideal for high-volume production. This process is key for adding functional features like bolt holes and slots, enhancing part utility and assembly.
Metal Stamping Materials
Worthy Hardware could stamped the following popular materials, if you have other brand, just send us for quote.
Material Type | Popular Grades Suitable for Stamping |
Steel |
– Cold Rolled Steel (CRS) – Hot Rolled Steel (HRS) |
Stainless Steel | – 301,304, 316, 410, |
Aluminum | – 1100, 3003, 5052, 6061 |
Copper |
– C11000 (Electrolytic Tough Pitch) – C26000 (Cartridge Brass) |
Brass |
– C26000 (Cartridge Brass) – C28000 (Muntz Metal) |
Bronze |
– C51000 (Phosphor Bronze) – C93200 (Bearing Bronze) |
Nickel Alloys | – Alloy 200, Alloy 400, Alloy C276 |
Titanium | – Grade 1, Grade 2, Grade 5 |
Metal Stamping Design Guidelines
Metal stamping is a complex process that can include a number of metal forming processes — blanking, punching, bending, and piercing, to name a few. Our engineers with more than 20 years in this filed would like to recommend you how to design the important dimension.
Hole Diameter
The minimum hole diameter should be equal to or greater than the material thickness. For instance, if using 1mm thick material, the hole diameter should also be at least 1mm.
Edge-to-Hole Spacing
The minimum edge-to-hole spacing should be at least 2 times of the material thickness. For materials 1mm thick, for example, the distance from the edge of the material to the edge of any hole should also be at least 2 mm.
Forming Bends Near Holes
It’s recommended to place bends at a minimum distance of two times the material thickness away from any hole. For example, with a material thickness of 1mm, bends should be positioned at least 2mm away from the nearest hole edge.
Notches and Tabs
For notches and tabs created through metal stamping, the minimum width should ideally be equal to or greater than 1.5 times the material thickness, ensuring structural stability and manufacturability. Additionally, the minimum length of tabs should be at least twice the material thickness.
Corners
Corner radii should be at least equal to the material thickness to reduce stress concentrations and enhance part durability. Sharp corners can lead to cracking and material failure, especially in brittle materials.
Bend Height
The minimum recommended bend height for metal stamped parts should be at least three times the material thickness. For instance, with a material thickness of 1mm, the bend height should be no less than 3mm.
Metal Stamping Application
Whether for electronics, automotive, aerospace, or medical applications, metal stamping stands as a cornerstone, offering versatility in producing high-volume, repeatable, and reliable products.
- Automotive body panels
- Electrical connectors
- Medical device components
- Aerospace fasteners
- Metal brackets
- Enclosures for electronics
- Heat sinks
- Engine components
- Battery contacts
- Appliance housings
- Decorative trim
- Lighting fixtures
- Metal keys and buttons
- Washers and clips
- Electrical Busbars
Our Equipment And Capabilities
- 25 tons to 500 tons high speed punching machines
- Laser cutting machines
- CNC Machines with 3 axis and 5 axis
- In-Housing tooling with EDM capabilities
- Max thickness could reach to 10mm
- Multiple materials
- Welding and PEM Fastener Insertion
Customer Testimonials
In the past 25 years, our clients are all over the world, including the world’s top 500 companies such as Jabil, ABB, Medtronic and so on.
Do you want to know what our customers say about us? Let’s take a look.
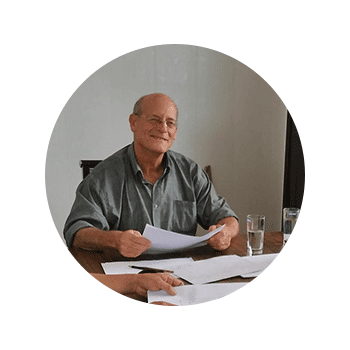
Justin, CEO of a lighting company
With most factories, I have a moment of fear before I open their boxes. Will the components be made correctly? Do they care about quality? It is often a war. And Dennis has to fight the war, treating most factories like small children!
But, not your company. You’re company is world-class. You make beautiful components! Thank you very much for your hard work. We will work together for many lifetimes!
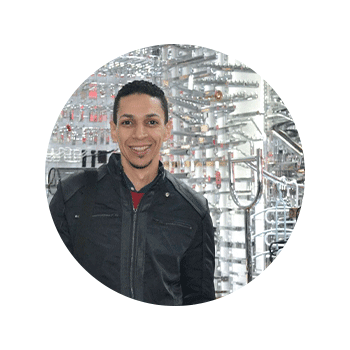
David, General manager for a family owned business
Metal Stamping Projects
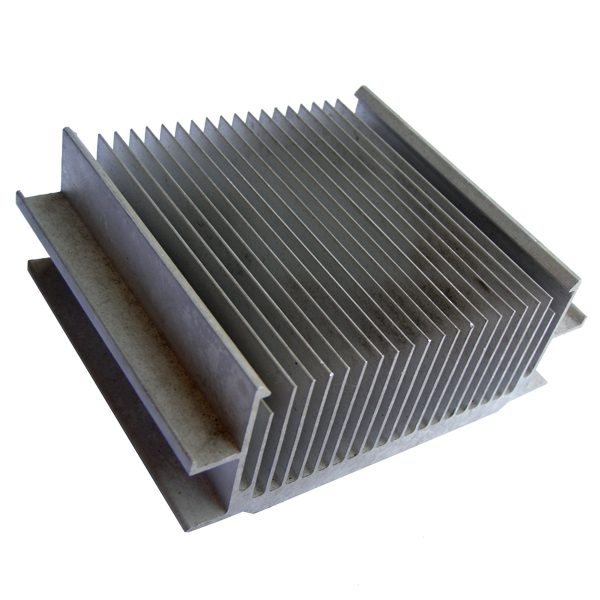
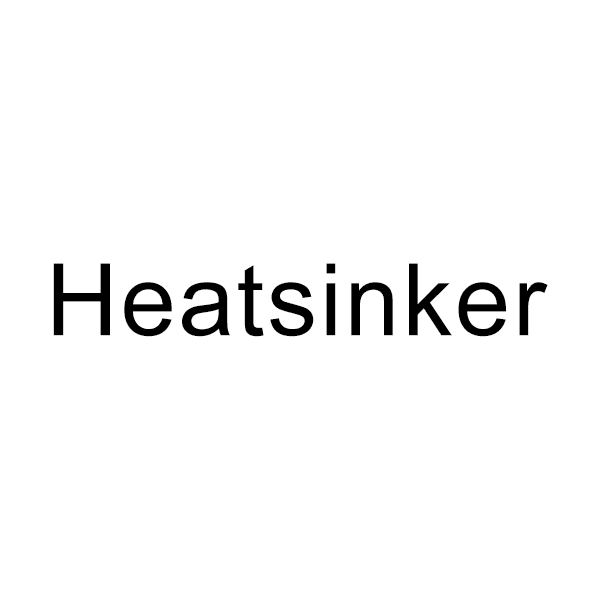
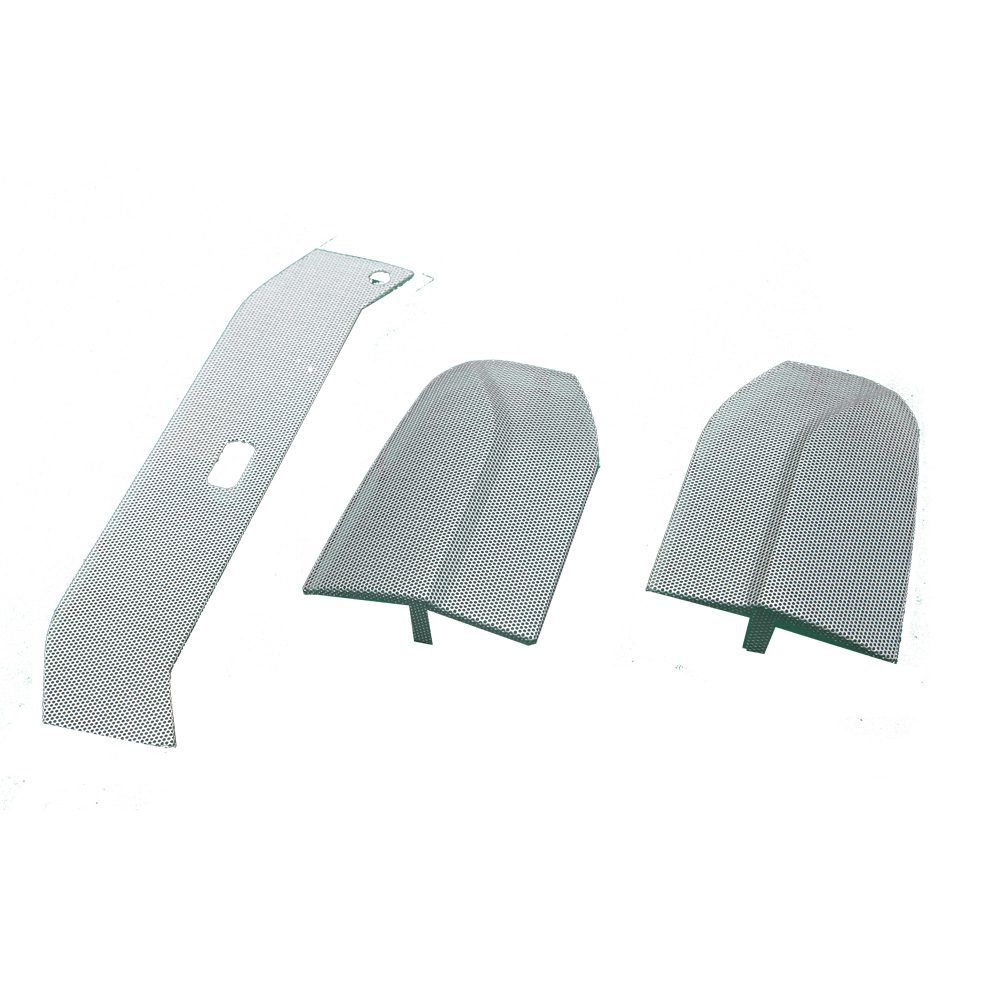
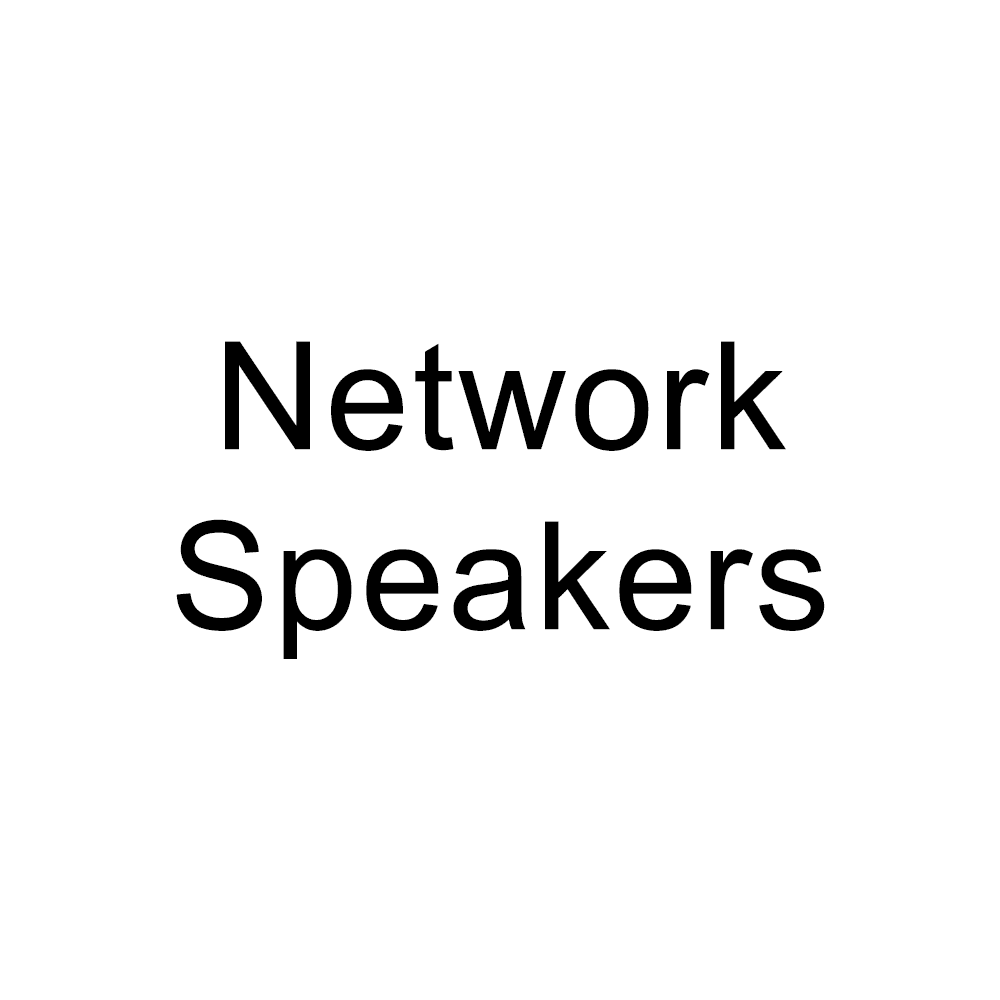
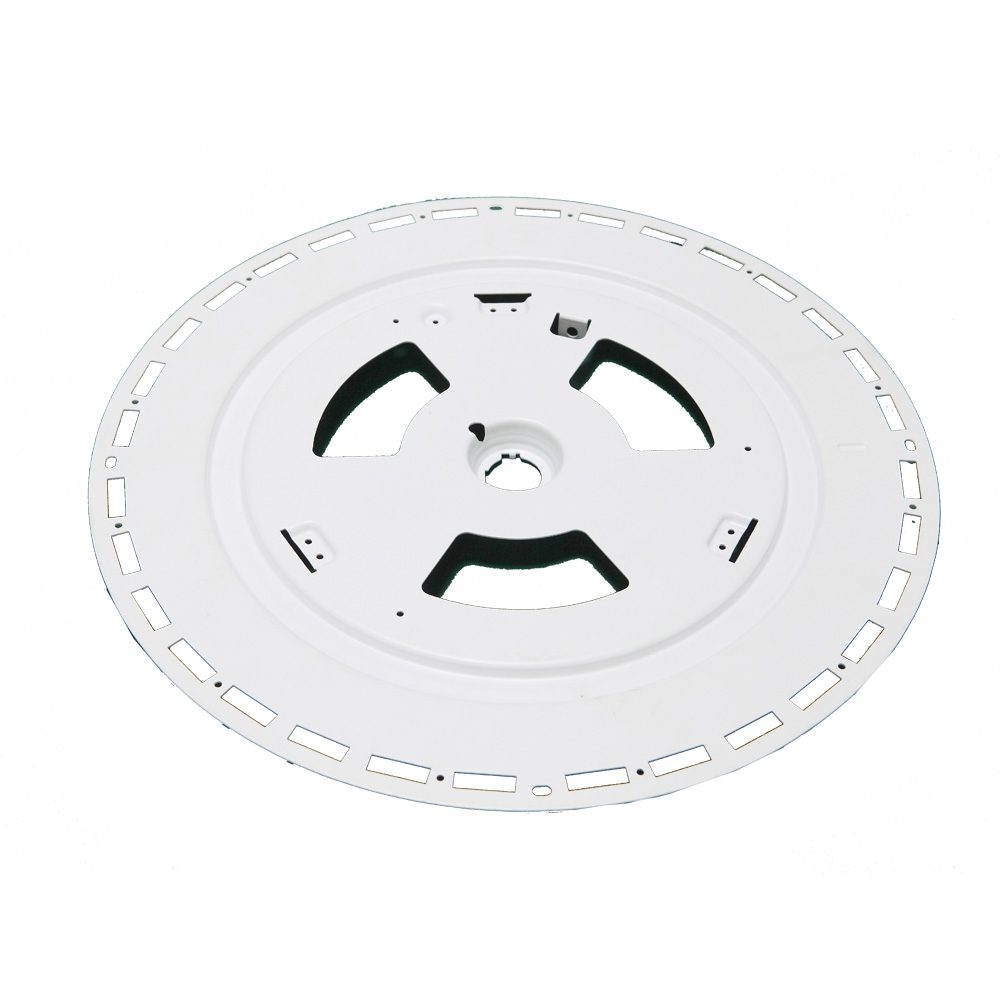
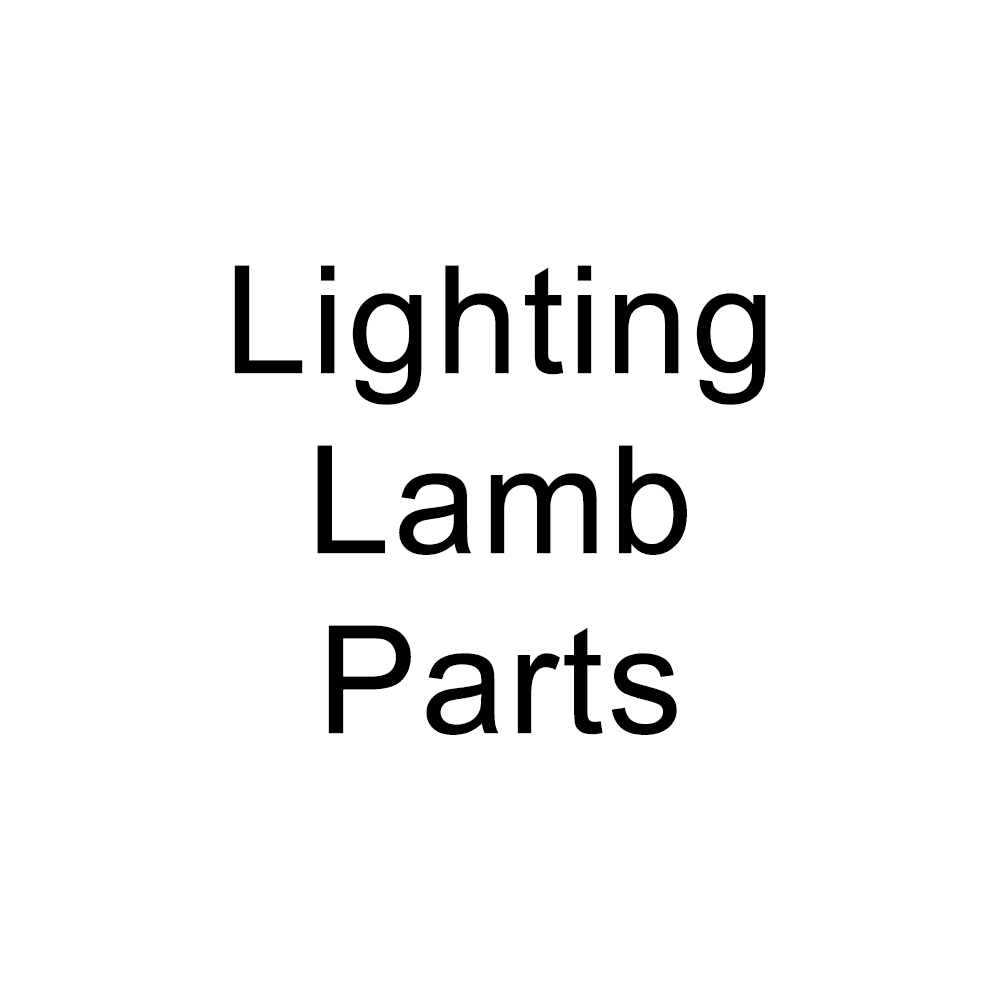
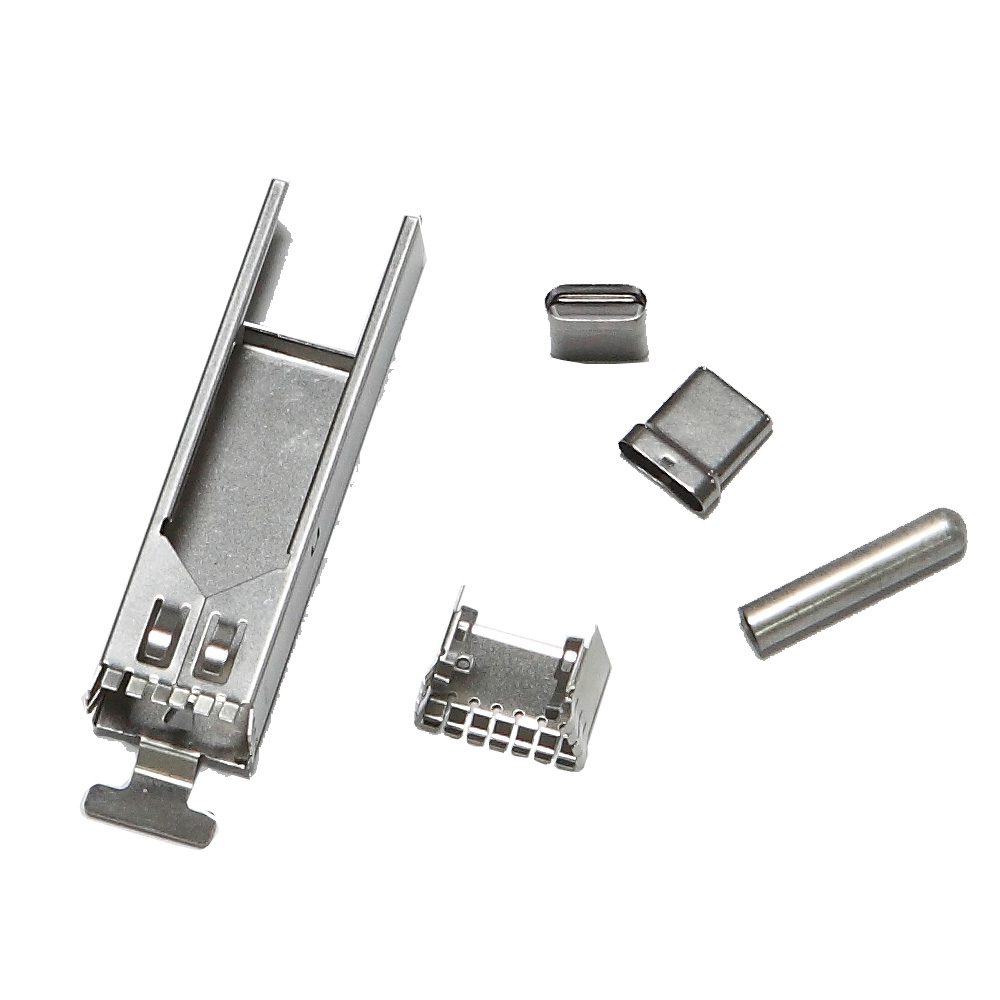
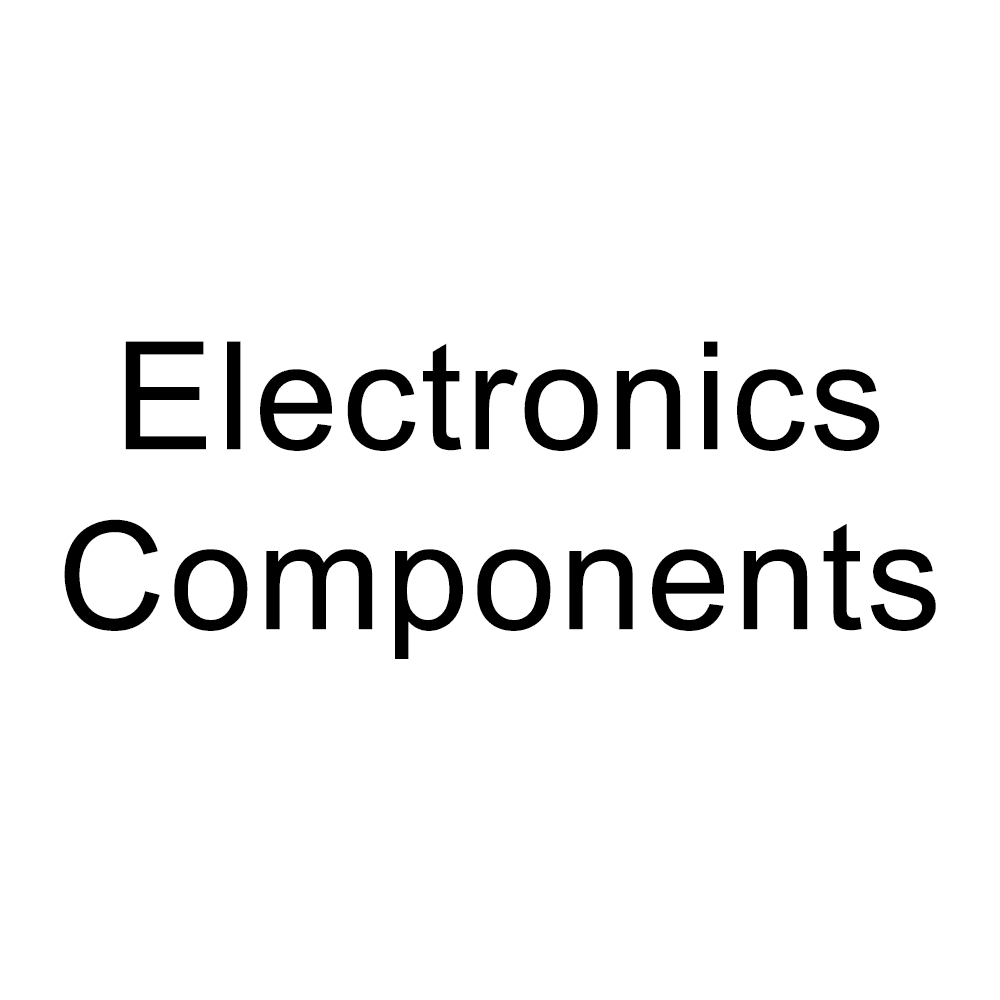
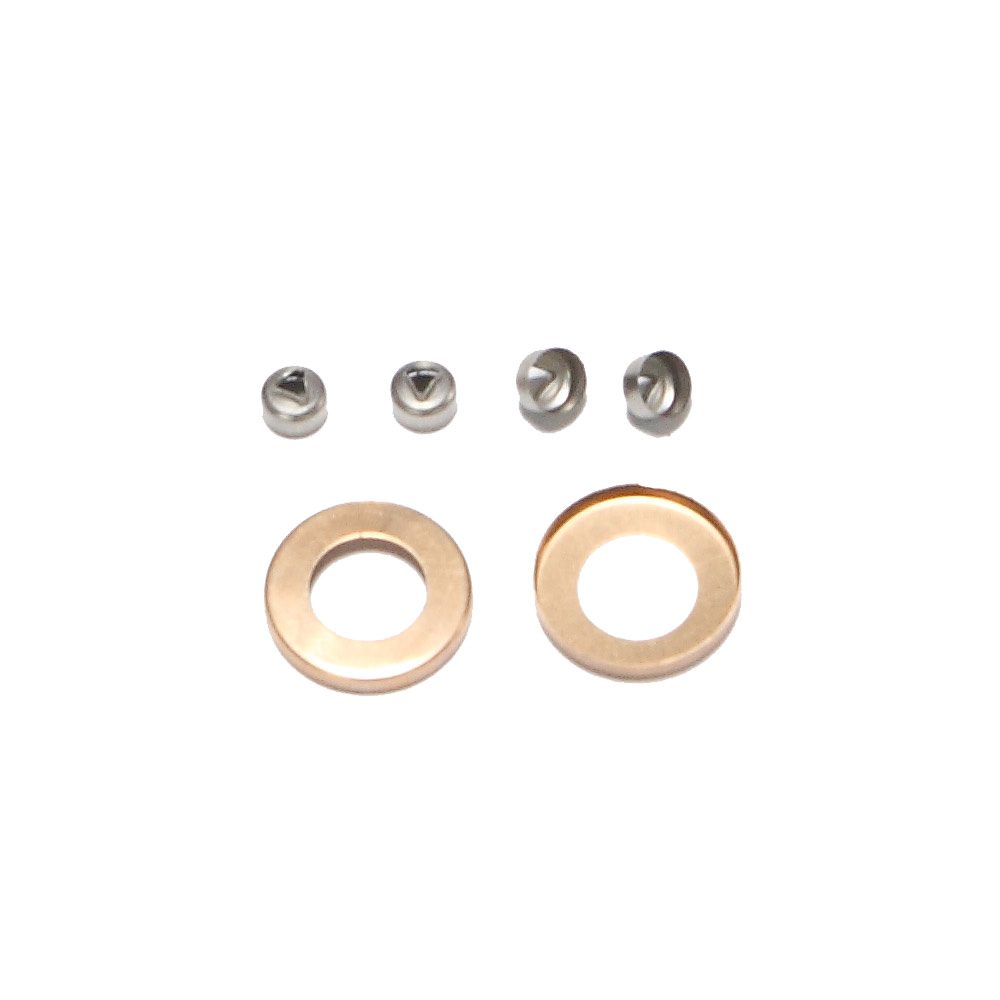
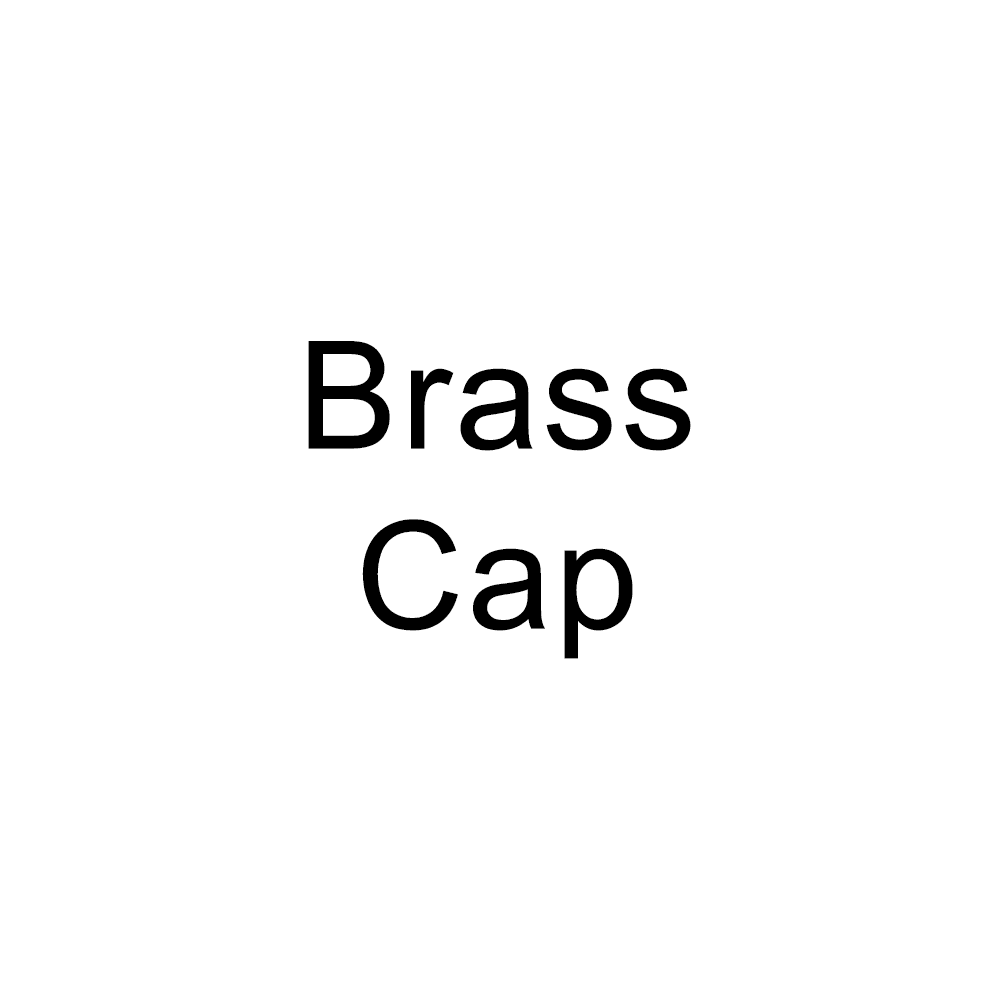
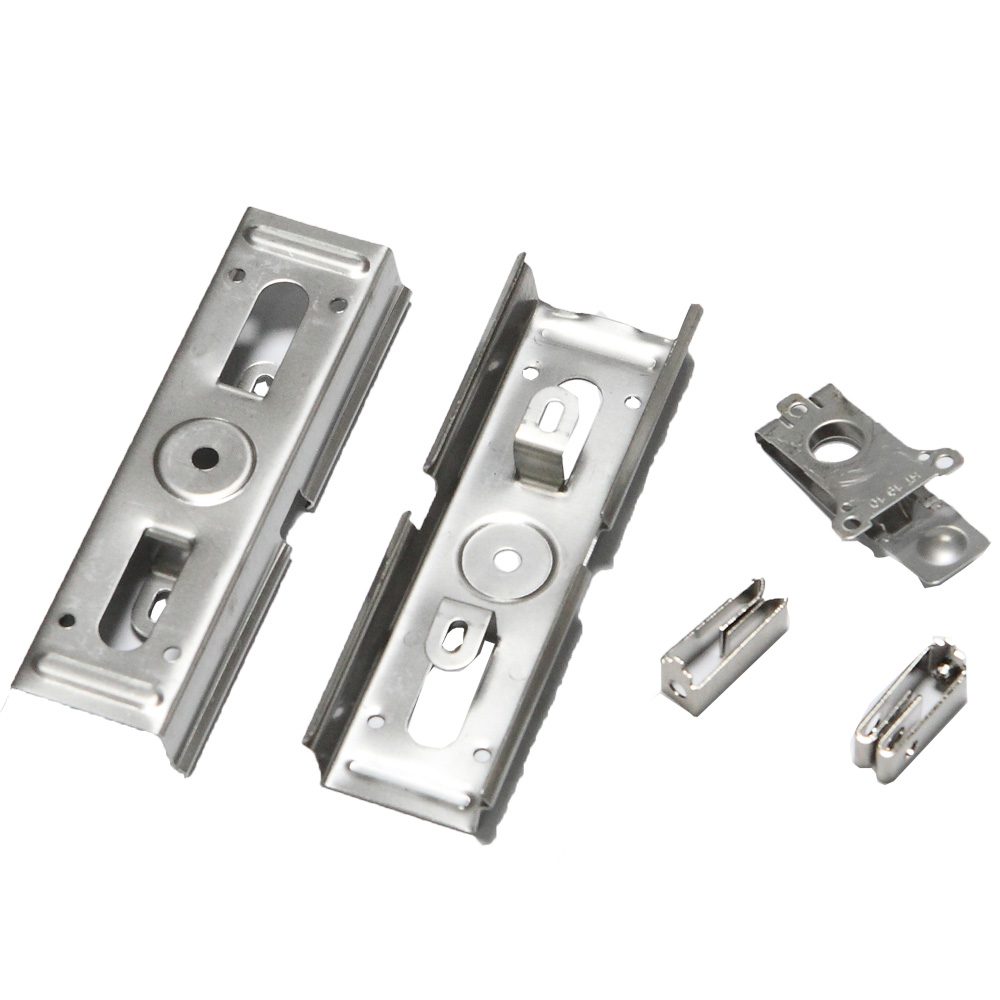
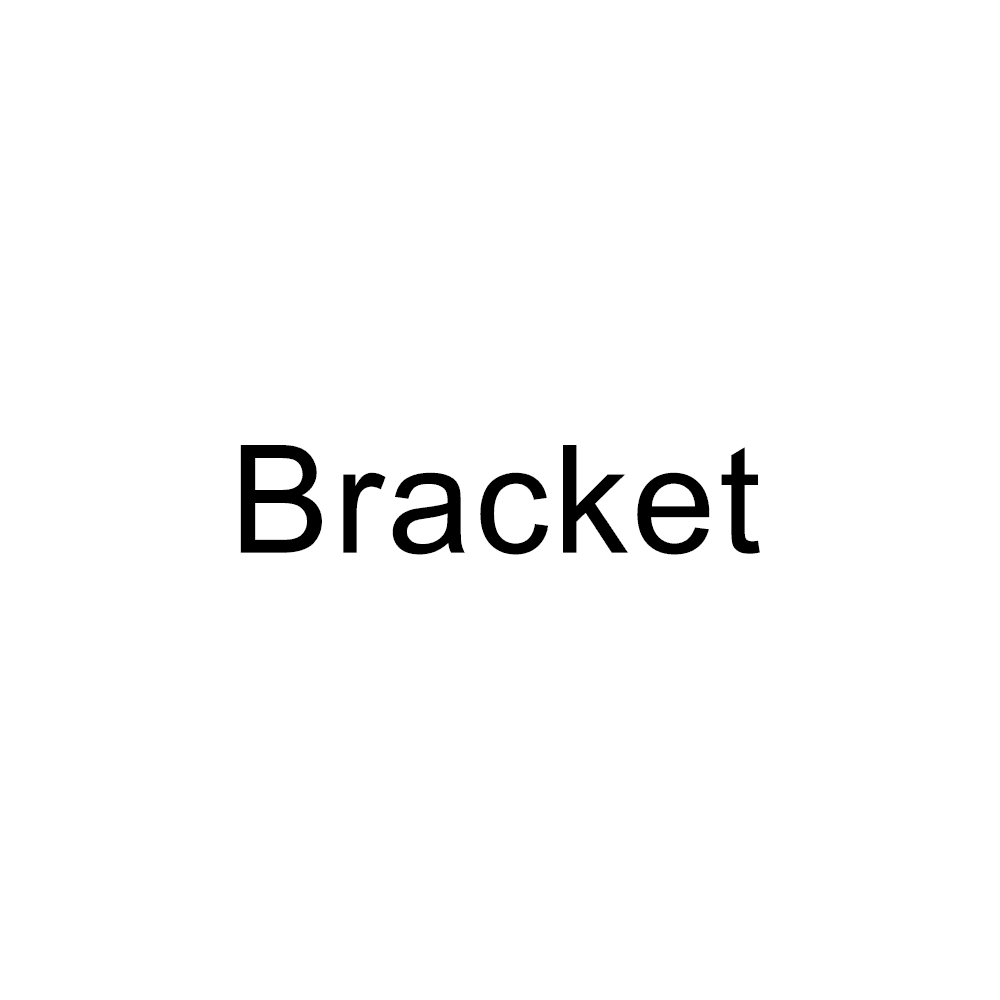